Motors for Aerospace Application
Megh Neel has mastered the design & construction of CORELESS, ZERO-COGGING permanent magnet synchronous machines. Megh Neel has developed models that can be used to accurately design & construct coreless, zero-cogging machines for aerospace application.
|
|
The video to the left shows a 5HP, 800 RPM, core-less, zero cogging PMSM machine. Notice that the shaft rotates smoothly without any cogging.
Coreless, zero cogging permanent magnet synchronous motors (PMSM) offer specific advantages in aerospace applications due to their unique design. Here are some ways in which coreless, zero cogging PMSM motors can be beneficial:
|
Reduced Weight: Coreless motors typically have a lower mass compared to traditional motors with a core. In aerospace applications where weight is a critical factor, such as in drones or satellites, the use of coreless motors can contribute to overall weight savings, enhancing fuel efficiency and mission capabilities.
Higher Power Density: The absence of a core allows for a more compact design and higher power density. This is advantageous in aerospace applications where space is limited, and the power-to-weight ratio is a crucial consideration. Coreless motors can deliver high power output in a smaller and lighter package.
Improved Dynamics and Responsiveness: Coreless motors tend to have lower inertia, which results in improved dynamics and responsiveness. This is particularly important in aerospace applications that require rapid and precise changes in motor speed and torque, such as in the control systems of unmanned aerial vehicles (UAVs) or robotic systems.
Enhanced Precision and Accuracy: Zero cogging in PMSM motors ensures smoother motion and eliminates the periodic variations in torque. In aerospace applications where precision and accuracy are paramount, such as in satellite positioning systems or scientific instruments on spacecraft, coreless, zero cogging motors contribute to better overall performance.
Reduced Electromagnetic Interference (EMI): Coreless motors may exhibit lower electromagnetic interference compared to motors with a core. In aerospace applications, minimizing EMI is crucial to prevent interference with sensitive electronic equipment on board, such as communication systems, navigation systems, and other avionics.
Durability in Harsh Environments: The absence of a core can make coreless motors more resistant to certain environmental factors, such as temperature extremes or vibrations. This durability is advantageous in aerospace applications where motors may be subjected to challenging conditions during takeoff, flight, and landing.
Maintenance and Reliability: Coreless motors, by virtue of their simpler design, may require less maintenance and have fewer components prone to wear and failure. This is advantageous in aerospace applications where maintenance access can be difficult or impossible, such as in deep-space probes or long-endurance UAVs.
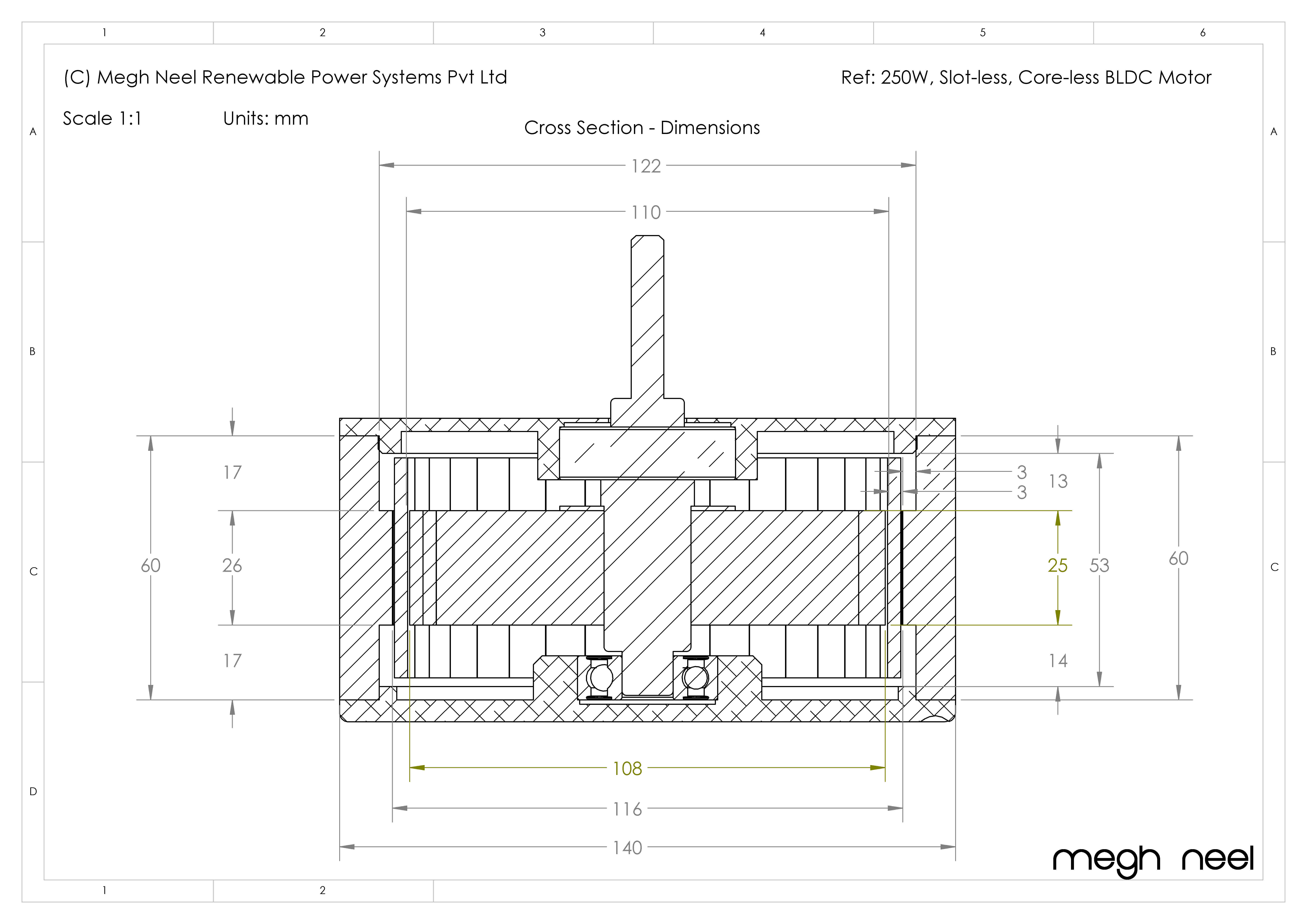 |
The above diagram shows a cross-sectional view of a 250W, 3000 RPM, core-less, zero-cogging PMSM
|
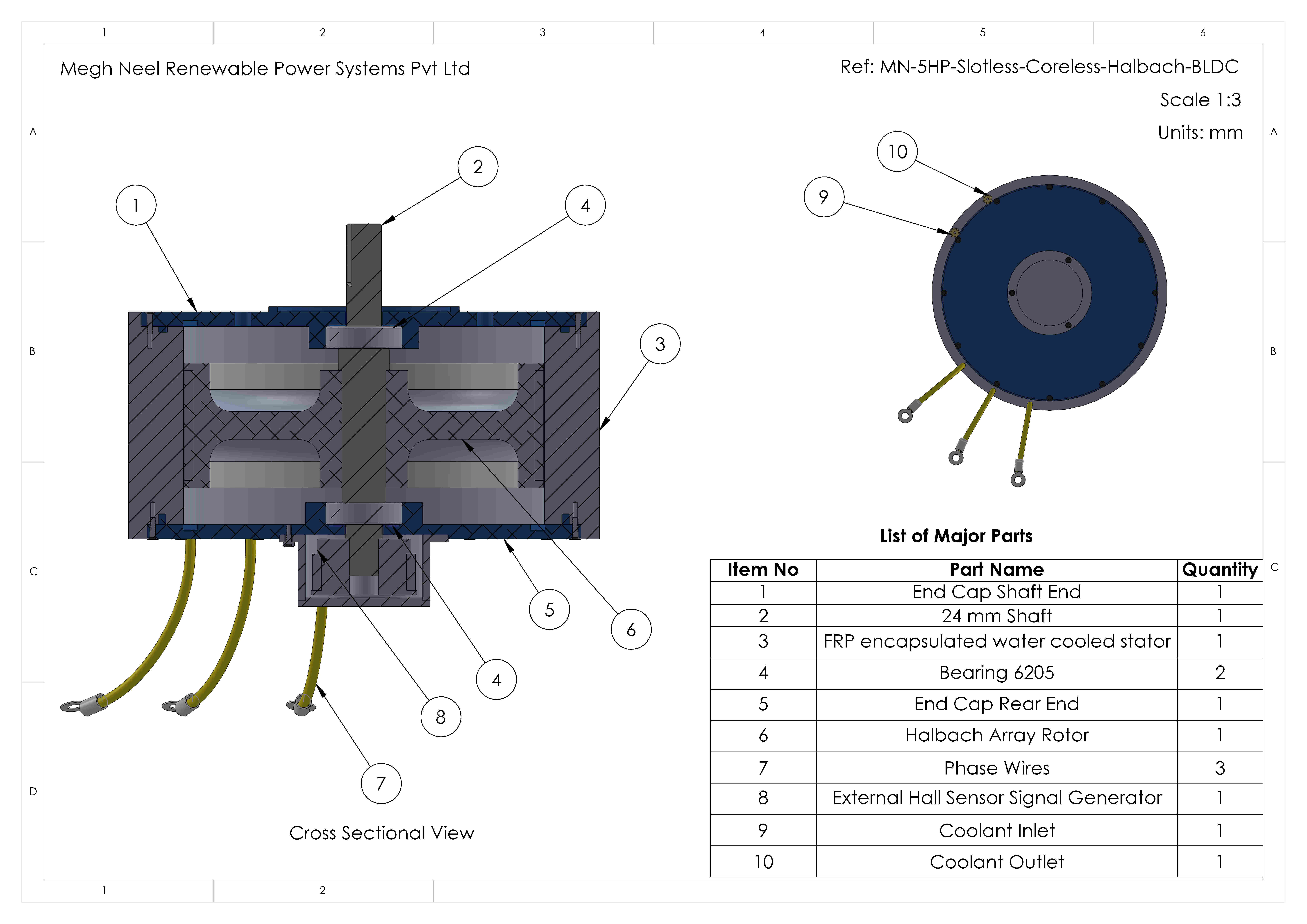
A cross-sectional view of a 5HP, 800 RPM, core-less, zero-cogging PMSM
|
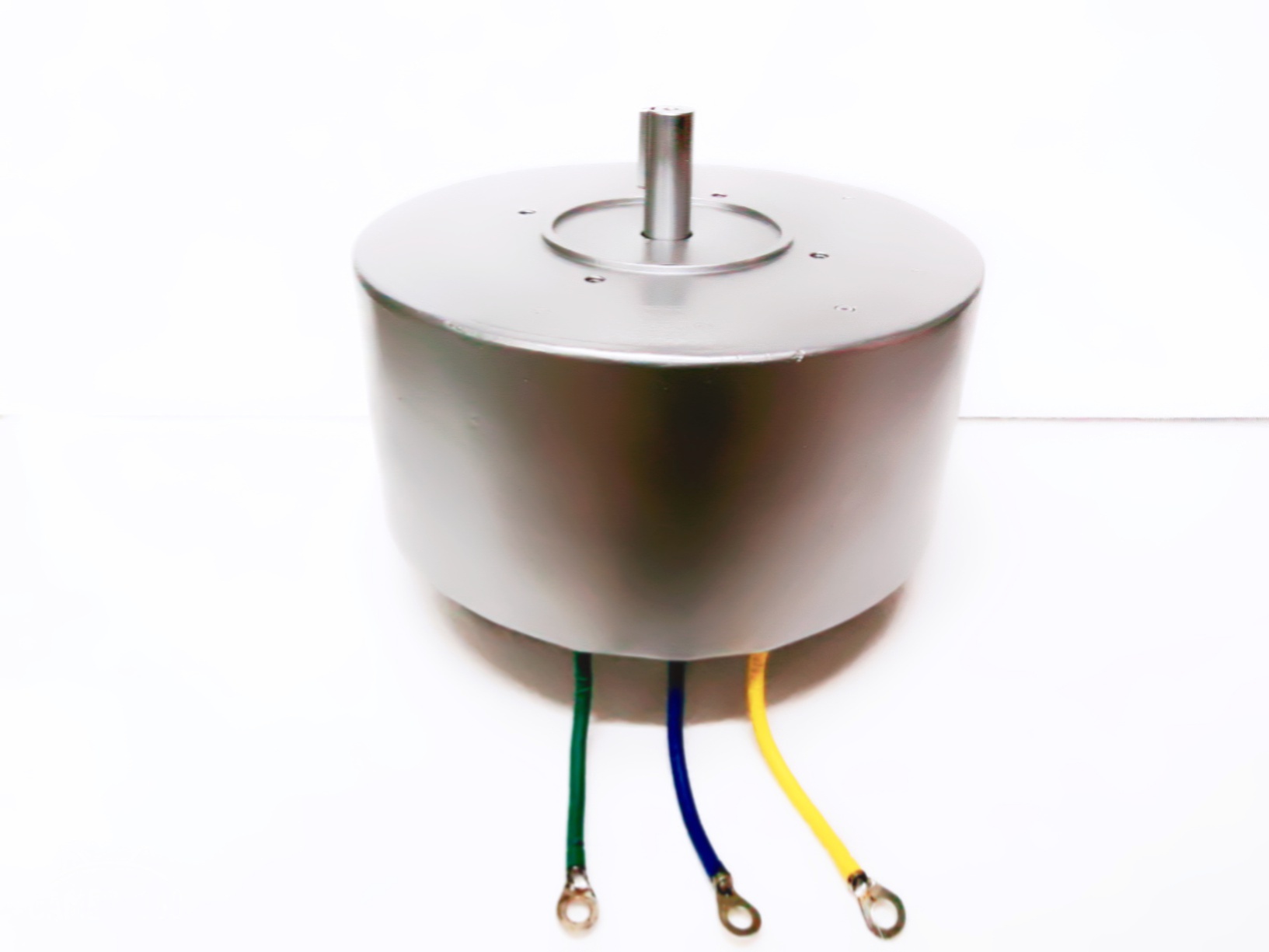
A fully assembled 5 HP, 800 RPM, core-less, zero cogging machine
|